Achieve your goals with the Kaizen Method

Setting an ambitious goal and trying to achieve it quickly is a common mistake in entrepreneurship. Trying to change things quickly increases the risk of failure. It’s better to focus on small but regular efforts.
This isprecisely the principle behind the Kaizen method, inspired by Toyota’s Lean philosophy. So what exactly is it?
Sommaire
Definition of the Kaizen method
First of all, you need to understand the meaning of the word ” kaizen “. It’s made up of two Japanese words, ” kai ” meaning change and ” zen ” meaning better. Kaizen therefore translates as ” change for the better ” .
In the business world, Kaizen means ” continuous improvement “, the basic principle of the Kaizen method. This approach came straight out of the Toyota factories in Japan in the 1950s. Launched by Taiichi Ono, it was intended to help rebuild industry after the war .
But it didn’t really catch on until around 1985. At that time, Taiichi Ono decided to found the Kaizen Institute. Its aim was to help companies implement this lean methodology.
The Kaizen method first appeared in the manufacturing industry. Today, however, it is used in a wide range of sectors. This quality management solution has already won over a number of large and small companies for its effectiveness.
The principles of Kaizen
TheKaizen method is really astate of mind. It is based on the following key principles:
- Avoid striving for perfection: with this approach based ona culture of improvement, perfection is not an objective . When it comes to problem solving, there is no such thing as a perfect solution. You have to take things one step at a time. Continuous and progressive improvement of your approach optimises your chances of success.
- Identify the cause of the problem using the 5 Whysmethod .
- Learn to prioritise problems: make changes taking into account the order of priority.
- Empower your employees: everyone can play a part in the continuous improvement process.
- Focus on low-cost solutions, which means you should avoid reinventing everything.
- Make decisions taking into account the opinions of several people.
- Remain reactive so that you can act immediately.
- Launch corrective actions as soon as a malfunction appears.
The 5 “whys” of the Kaizen method
Applying a continuous improvement approach requires you to identify the cause. Otherwise, it will be difficult to make operational improvements to achieve results. To find the source of the problem, the Kaizen method encourages you to ask the “why” question 5 times .
For example, the product was not developed within the allotted time. So you ask the question: “Why? The answer might be that the team is behind schedule. Then you ask “why” again, and so on.
By using this method, you can gain a clear understanding of thecause of the malfunction. You can then develop a more effective management system or lean approach. This way, the next time you carry out a similar project, you’ll have a better chance of succeeding.
The tools of the Kaizen system
The Kaizen method is a quality approach that brings together several quality management tools.
The 5S method
This is aproductivity method and its name is inspired by the first 5 letters of the following Japanese words:
- Seiri or “order”: you need to create a well-ordered workspace by eliminating unnecessary items,
- Seiton or tidy: everything must be in its place so that it can be retrieved quickly and easily,
- Seison or shine: you need to create a shiny working environment by scheduling regular cleaning,
- Seiketsu or standardise: you need to put in place standardised and consistent working practices,
- Shitsuke or maintain: once the 4S have been put in place, you need to ensure that they become the new management system in force within your company .
It should be noted that the 5S method enables a workplace to be properly organised in order to achieve operational excellence.
SMED or Single Minute Exchange of Dies
This isanother of thecontinuous quality improvement methods used in a Kaizen process. SMED is applied to encourage rapid tool changes. So if you need to use several machines during the production of a product, this method will save you time.
Lean management
With the Kaizen method ,waste is a thing of the past. That’s why production must be adapted to the customer’s needs. This will help you avoid inefficiency and make your project more profitable. If this is your objective, Lean Management is the management method to use.
Lean manufacturing
Lean manufacturing is another continuous improvement tool that you can adopt. Its principle is to eliminate low value-added activities. It therefore makes it possible to :
- Improve the production process,
- reduce production costs,
- Optimise your company’s competitiveness.
The TQP or total quality management method
This corporate quality managementmethod requires the involvement of all employees. It also enables you to combat waste and improve the end product.
Lean logistics
The principle of Lean Logistics is to put together a well-trained, competent team. It must be made up of people who are prepared to deal with dysfunctions by adopting a process of continuous improvement in supply and transport.
The Kanban method
Another method, the Kanban method aims for continuous improvement through the use of various visual signals. Its use guarantees :
- save time,
- increase the efficiency of your staff.
The Deming wheel or PDCA cycle
Originatingwith Walter Shewhart, the PDCA cycle is a method that was democratised by W. Edwards Deming. It is one of the best tools for continuous improvement and comprises four stages :
- plan, or establish an action plan based on the main objective,
- developing (Do) or carrying out the established plan
- checking, or carrying out tests to identify the necessary improvement practices,
- act, or adjust.
Thanks to this methodology, you can easily make the changes you need to manage your project successfully.
The Six Sigma method
In your desire toimprove your company’s performance ,you can also rely on the Six Sigma method. This process improvement tool is very popular with players in the industrial production sector. It is made up of two methodologies, including :
- the DMAIC approach, which has 5 phases: define, measure, analyse, improve and control,
- the DMADV approach, which also comprises 5 stages: define, measure, analyse, design and review.
Implementation of the Kaizen method
By using these different tools, you can apply the Kaizen method with ease. The process takes place in 6 stages:
- Identify an improvement objective
- Seek new ideas by asking your staff for their opinions
- Break the objective down into several sub-objectives
- Plan the tasks required to achieve each sub-objective
- Carry out tests to identify the progress of the project
- Adapt the schedule according to the problem that arises or move on to the next objective
The benefits of the Kaizen method for your company
What are the advantages ofusing the Kaizen method ? Here are some of the advantages of this Lean approach:
Reduced cost and risk
As a reminder, the principle of this approach is to make modest changes. Then you analyse and test to see if the changes have been successful. It’s a low-cost process, and there’s no risk involved in applying it.
Changes accessible to all
Kaizen management allows everyone in your organisation to understand and adapt to the process. If a member of your team encounters problems, they can make changes that will enable them to carry out their work successfully.
A personalised team process
You should know that the Kaizen method can work in a group. So it’s a great way to build real teamwork. Your employees can even identify the continuous improvement tool that will help them evolve .
A process that guarantees profitability
With the Kaizen method, you can make concrete improvements that could boost your profitability. This lean approach enables you to :
- optimise the efficiency of your team
- optimise customer satisfaction by promising them quality assurance
- improve the production process,
- avoid overproduction,
- optimise productivity,
- improve the quality of the finished product.
Combining the Kaizen method with business software
Have you decided to apply the Kaizen method? For the process to be a success, you first need to choose the right methodology. You also need to set up an effective communication tool. This will enable all the operators to follow the progress of the project and make relevant suggestions if things get stuck.
Itshould be emphasised that the Kaizen method can be applied methodically to all aspects of an organisation, including purchasing management. Weproc software has been designed to facilitate the implementation of this method in this context. Our solution simplifies the collection and analysis of your business data, identifies inefficiencies and helps you frame your internal procedures. In this way, Weproc fits in perfectly with initiatives to implement a Lean Purchasing approach within modern businesses.
Want to learn more about our procurement management software Weproc? Contact us or request your free 15-minutes demo below!
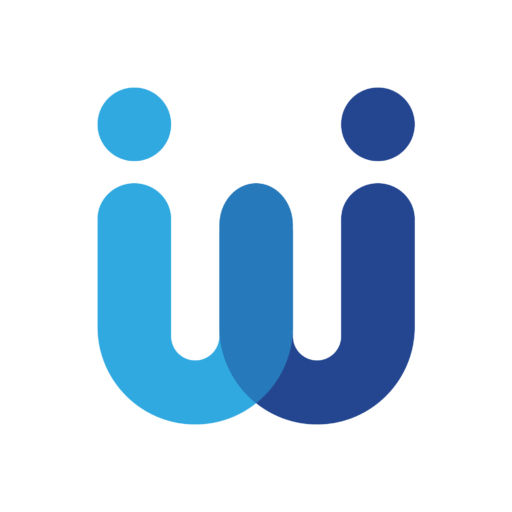
Weproc is a SaaS software specialized in digitizing the procurement process of companies. From purchase requests to supplier invoicing, through the validation process, Weproc is designed to simplify the purchase management of SMEs and mid-sized companies by centralizing all purchase-related activities.